INDYCAR MEDIA CONFERENCE
May 21, 2021
Indianapolis, Indiana, USA
Press Conference
THE MODERATOR: Good morning. I think of all the great traditions at the Indianapolis Motor Speedway, all the great awards that have happened over the many years here, this is certainly one of them. Looking at all the names that are on the side of the Louis Schwitzer Award, all the great innovations that have taken place, the great men and women that have been honored. That continues in 2021.
It's with my honor to hand things over to Steve Holman, chairman of the Louis Schwitzer award for another great honoree.
STEVE HOLMAN: Thank you all of you for joining us after this crazy year for the 54th annual Louis Schwitzer Award, presented by SAE, Indiana section, sponsored by Borg-Warner.
First, a quick mention of last year's award winner, the Aeroscreen project. Our work was done remotely with Zoom meetings mostly because it was a huge project involving team members from Italy, Austria, England, California, here in Indy. That group was involved in creating one of the biggest safety improvements in years, which has already been credited with saving several drivers from serious injury.
Conversely, this year's recipient is a single individual with a singular vision. He started his career path with a degree in chemical engineering, with a specialization in the then new field of biomechanics, as it was called then. Next, a medical degree followed by a renowned career in orthopedic surgery, especially relating to race driver injuries.
After seeing the damage being done to drivers, he had a vision to use the unfortunate, inevitable crashes to develop a new system to record the relevant data: speed, angle of incidence, deformation, chassis and human g-forces, extent of injuries. No longer was it just, Oh, that was a hard hit. The value of that data cannot be overstated.
Over 20 years of such data, it's driven the continuous improvement in race car strength, energy absorption, and injury reduction.
Our 2021 Louis Schwitzer award winner is Dr. Terry Trammell.
DR. TERRY TRAMMELL: Thank you. I'm very honored to have received this. I want to express my appreciation to the Louis Schwitzer Award committee for awarding me this honor. It was unexpected, to say the least.
I want to thank Borg-Warner for sponsoring. The opportunity, I'm a member of the SAE and depend on them, I use their library a lot. It's part of a teaching thing that I did. One of the first things you do when you work on project is go to the library, find out who has already done it. I depend on that often. I'm appreciative of the SAE for being the SAE.
The beginnings of my engineering education and what I intended to do to pursue a path in biomechanical engineering, actually was doing a senior research project for industry when my adviser suggested if I was going to pursue this I should go to medical school. I'll save the real story for Saturday night, kind of skip over that.
I took his advice, I went to medical school. The closest thing I could find to biomechanical engineering in medical school was orthopaedic surgery. When you really think about it, a large number of orthopaedic surgeons have an engineering background. One of the core principles throughout an orthopaedic residency is regular education in biomechanics. When you're putting hardware in people, it's a good idea to know how heavy the hardware has to be, how many screws, how long a plate, what kind of material, so on and so forth. Without really knowing that's we're doing, that's what we do every day.
That fit into this nicely. In 1992, if any of you recall what happened that year, it was extremely cold for the month of May. The tires were like hockey pucks on the track. Every time the cars would start, there would be a crash.
I normally stayed down with the safety truck and the ambulance in the short chute between one and two. If somebody got hurt, I'd listen on the radio. The ambulance would call in and I'd go back to the care center to take over my role as an orthopaedic surgeon.
When that weekend was over, I finally got home, my clothes from the track were still in a plastic back where I put them when I switched into a scrub suit, soaking wet, like they'd been in the rain. My wife goes, How did that happen? I said, Well, I was running back and forth. I figured I was the only person in this facility that was sweating on that day. Not even the drivers were that wet.
Anyway, that got the start. I had taken care of a driver driving the Oldsmobile Intrepid of Tommy Kendall. Earlier that year I had taken care of him from an accident he'd been in. I was funded by and put on the track by General Motors Motorsports Technology Group. I got a call from an engineer that I knew of, a guy named John Melvin. John said, I think we can help you. If you'd like help, I'm available. I said, I know I need help. I'm not sure exactly what help I need, but let's talk.
We met out here on the Tuesday after Memorial Day, started measuring witness marks from the tire skid marks, length of mark on the wall, how far apart the posts were, angles, so on and so forth. I looked at the cars. I looked at all the x-rays as they came in. I started measuring things, the normal length of the leg, how much it shortened.
The first two things that came out of that was General Motors came up with a computer simulation of the accident, which was Jeff Andretti's accident, which was one of the first computer simulations of a race car that I think anybody ever did.
The second part of that was, we figured out how much more length we'd need in the nose of the car before intrusion got to the driver's feet, and passed that information along to CART in those days, I was the director of medical services for CART. That got sent through to Kirk Russell. Kirk said, Okay, we'll make the nose go that much longer. They added it to the front end of the car. That was the beginning of actually taking something medically and treating it with engineering thought processes and principles and coming up with a workable solution that would protect the driver from injury and put it on a race car.
From that point in time, it's been one continuous evolution of bigger, better, faster, safer. The number of people that have helped do that along the way have really been quite incredible. I mean, one of the most beneficial things for the drivers, the SAFER barrier, was first put here, funded by Tony George. I ended up literally on the auction block when CART went bankrupt. I was an asset, my contract was going to get auctioned. I went to Tony and said, Do you have a problem you think I can solve? I'd like a job. I got a fancy presentation. Tony looked up over his glasses and said, Okay. Okay? Okay. Go across the street and tell them you work for us. I said, Okay.
That's where the seats came from. There was a rash of spine fractures that had occurred in CART, INDYCAR, IRL, Toyota Atlantics. They all had great similarity. So we approached it directionally. First thing you do is gather all the data. We looked at which scenario most frequently caused a fracture and why. That was the first thing that we solved. We did that through some FEA analysis that Delphi helped us with. We went to Delphi. I can't even begin to think how many sled tests we did to figure out what the dummy was doing in the car. We found out that the hybrid three dummy wasn't very compatible with what we were trying to do, so they bought us a Thor, which at that point in time there were two. Ours became special because we broke him several times right off the bat, had to have new pieces made that were battle hardened to withstand the g-forces. It all evolved from knowing what those g-forces were.
Go backwards back to '92. John Melvin, when we started doing this, I'd go up to Michigan to the test facility there regularly, we'd run sled tests. We'd look at information that we kept because we kept really good records of all the crashes, anything we could measure, we did.
John said there's a company that makes a recording box that's a scientific instrumentation. Like when they send a computer overseas or other electronic components, they put this box in the crate. When the part arrives to its destination, the first thing they do is download that box to see what accelerations it's seen in transit. If it's been dropped or fallen over or handled roughly, then they wouldn't accept it because the box would show them that.
We took those boxes. The guys at GM wrote some software to make it work. We put it in a car. That was in '93. The first few times that the car crashed out here, it was over 50Gs. Not so much I did, because nobody really knew who I was, but John got a whole lot of hate mail that that was not survivable, that our information had to be wrong because the driver couldn't survive that. It took us a long time to explain to people that box measured what the chassis saw, not what the driver saw.
From that, then we're going to have to figure out how do we know what the driver saw. That's where the ear accelerometers came from. The best thing we can do is put them in the ear phones. At that point in time a company had come along with these little chips that measured in one axis in each direction. We had the three axes covered in both directions. Six directional ear accelerometers in both ears.
Over the years we've collected a vast amount of data for every crash. Every crash we download the box, we get the earpieces, confirm that they still work, that they were working at the time of the incident, correlate the crash box data with the ear accelerometer data. If the driver is injured, we start to, just like you would a crash investigation, find where the major injury vector came from, what that amount had to be in order to produce the result that it did, and use that information to change the way the car did.
That led to the seats, to start with, the foam and contour of the seats. I don't know if you know or not, but Dallara INDYCAR 12 has crash foam built into the chassis. The driver doesn't even know it's there. There's basically three inches behind his back, 30 millimeters in the floor. It's covered with a real thin carbon fiber panel. Then they build the seat out of the same foam and put it on top of that in the car.
We have that pretty well covered. That combination of things drastically reduced the number of spine fractures that we were seeing from a rear impact.
We did some work where the car goes up in the air, comes back down. That was an award-winning SAE paper for vertical impacts. We were able to engineer how much foam we needed in the bottom. That's what we wanted in the Dallara 12, but they wouldn't give us that much room in the bottom of the car, pushed the driver too high. It's better than it was.
Then some of our hip injuries, hip and thigh, we were able to reduce the risk of that by side panels, which was a very interesting engineering project because the panel -- any of you that have anything to do with side intrusion in an automobile, passenger car, there's a point at which the padding becomes so stiff, it becomes the piston that causes the injury. It has to be soft enough that it actually keeps you from breaking your pelvis and your hip, but firm enough if you're a race car driver it doesn't let you bend sideways in the car when you're going around a turn.
We took our most objective test driver and put that in the car in Detroit the year that we were working on it, and had him drive several iterations of it. He would come in and say it's too soft, put another one in, I can't feel the car, oh, that's better. The solution was we took the foam and they ran a computer model. He ended up drilling holes in it that went part of the way through in some areas and changed in diameter and others that we could tune the foam to make it stiff enough that it didn't take away the driver's feeling from the car by having him sink into the side of the car, but soft enough it didn't hurt him when he hit something hard. That was really one of the best things that we've done because you had to please the driver as well as protect him.
That's kind of leads up to today. The amount of work and the number of people that have worked on the new ADR force system that went into the cars Tuesday for the first time ever, it was phenomenal what they had to do over the weekend.
They start with what would seem like the simplest thing. A lady, Vicky Lauks (phonetic), makes the impressions, the things that go in their ears that has the accelerometers in it. Although she has to scan and print, 3-D print the pieces, anybody that doesn't have an anatomically normal ear canal, she has to make by hand. In the last week, the second set starting on Monday, she's made over a hundred sets of earpieces. She's been here around the clock since Monday because she has to have the driver to do it, to test the fit.
The evolution of this box, an engineer I didn't even know we had, I kept saying what I needed. We started back a year ago, more than a year ago, by setting up a test matrix to prove that the new box and the old box would record the same loads the same way. They had to be within a very narrow variance, otherwise all of our old data would have been obsolete because it wouldn't have compared to the new. That was my first why. I got to have it this way. If the two boxes aren't the same way, I don't want the new box. They put together a program that satisfied my whim. We got the new box tested. It tested out the same.
Then she had to build all the new earpieces. They had to write all the new software. INDYCAR engineers did all of the software work. A lot of that took place in the middle of the night, 4 a.m. in the morning when it's 10 a.m. in Europe, doing it online because you couldn't travel.
The way it's wired to the box is totally different than it was. A couple of little things, for example, the radio goes through the same connector. There used to be two. So now the driver can tell that he hasn't plugged his ear accelerometers in because his radio doesn't work. Suddenly we don't have people forgetting to plug their earpieces in because they can't use the radio. It has a correct polarity. Actually this morning somebody is going around telling all the drivers to make sure they put the left one in the left ear plug, the right one in the right. They're different. I get the data back, I looked at it from yesterday, this is backwards. We went and looked, that's what had happened, the driver put his right ear plug sensor in his left ear. I didn't like what that did. The numbers were backwards.
All of that was done by one of the Penske people. They made the wiring harness and the loom on the prototypes. Then the part that I liked the least that somebody has to do is all the interface with the people that write the checks and give the okay to do it. One of the engineers, Darren Sampson, I didn't even know all this was going on in the background, if I don't get what I ask for, I ask again. If I don't get it then, I ask somebody else that can say okay. Just like your kid at home. You know how that works. They ask mom, then dad. They say, Daddy said. That's what I did for the last 30 years. If I don't get what I want from one person, I go find somebody else that can make it happen.
That's what Darren did for us, is he got the checks written, legalese done, so on and so forth. Why isn't this thing ready yet? Why can't we test it? Finally we did.
Yesterday was our first real test to the system. We had to rewrite software last night, update some things because we found a glitch in the system. Hopefully that's fixed. So that's what I do.
STEVE HOLMAN: Thank you. What Dr. Trammell was mentioning about the accident data recording systems dates back to the early 2000s when the Delphi unit became available. They actually won one of our Schwitzer awards. As of now or last year, that unit was essentially obsolete, needed to be replaced. That necessitated this new ADR system that Dr. Trammell was referring to.
Our committee this year was initially investigating that new system. We went and talked to Dr. Trammell to get his input on it. We could tell immediately he was a big source of the impetus for all the safety improvement over the years with all these accident data recording systems.
With that said, if you'd go ahead with a couple questions.
Q. Dr. Trammell, one of the better lines that came out of the movie Rapid Response is when you said your first 500 you came out here to work as a doctor, they put you in a first aid unit, all you did was treat drunks and sunburn victims all day.
DR. TERRY TRAMMELL: The police officer that got hit by a motorcyclist, and the motorcyclist that hit him.
Q. You said at that point if that's all you were going to do, you didn't have any interest in coming out here. What was it that eventually lured you?
DR. TERRY TRAMMELL: I'm from a motorsports family. My father worked for Perfect Circle. They sponsored dirt cars a lot. When I was a kid, we went to dirt car races. I was at the Hoosiers 100 before they had fences. You could just stand wherever. If nobody told you to move, you stood there. We all stood outside the fourth turn. It was a badge of honor to see who had the biggest bruise from the dirt clods coming off the track. You know how that would work these days.
I'd been here as a spectator a couple of times when I was hardly tall enough to see over the people standing in front of me. I liked the sport. I listened to every 500 from the time I was in grade school practically and could tell you the names of all the guys in the corners that were doing the broadcasts.
After the medical school experience, I'm not doing this any more. I lived next door to one of the photographers that was here all the time, Don Blake. Don would bring me along, I'd carry his bag. Every now and then I'd take a few pictures. I have the one picture I sold, got five bucks for it. I still have the $5 in a frame in my office as home. That was my career as a professional photographer, which was what I was supposed to be doing in 1981. I didn't know that I was going to be the trauma doctor that day. I didn't read the fine print in my contract. I ended up being there when Dan Ongias crashed.
The conventional wisdom at the time, it was a not soluble problem, treated by amputation. Fortunately I was mulling over this. I wasn't going to amputate it. It would turn black before I was going to take it off. There was a cardiovascular surgeon that did three tours in Vietnam. He walked by and goes, Do you need help with that? I said, He has a dysvascular extremity? He goes, That's no big deal. Let's take care of that.
In the operating room he said, You fix it so that the leg doesn't move, I'll fix the vessel, he'll be fine. I wouldn't call it fine, but he walks on it. I thought I'd get an opportunity to straighten it out better at some point down the road. He liked it just fine the way it was. So it's not pretty, but it works.
Q. Jack Brabham said when he raced here, there used to be a big crash every day in practice, guys getting airlifted to the hospital. It seems over time the evolution of this event, the safety of the cars, we don't see that very often any more. How important do you think that is that a lot of the stuff you've done, all the innovations that have come, has really helped make that less and less of a situation that we see?
DR. TERRY TRAMMELL: I stopped operating at the end of 2012 for a variety of reasons. That was the right time. I was at what I felt was the apex of my career, wasn't anywhere to go from there. My interests had changed from being in the repair business to now I'm in the prevention business. So if somebody gets hurt, I take it very personally because the means that we didn't prevent the injury, something we overlooked, underestimated or whatever.
That's what we do now. Every accident is investigated not only from the standpoint of did it cause an injury but what worked that prevented an injury.
If you want to see the best example of how these cars can protect the driver, go look at the first lap of the second race at Texas. There were seven cars involved, six that were disabled, that got hit multiple times. One car got hit once, the car that got through, the 48 car just had a little wing damage. Everybody else, it was like bumper cars. One of the cars got hit by the same car twice at the beginning and the end of the accident. How many different ways?
If you looked at the degree of destruction of the car and the fact that we had one driver that had a bruised knuckle, another one that had a sore knee, a little muscle strain from being spun around like a top several times, it was perfectly understandable. Yeah, that happens.
They worked. Do they always work? No. But we'd like to think they would always work.
THE MODERATOR: Good stuff. Congratulations, Terry. This is awesome.
DR. TERRY TRAMMELL: Thank you.
FastScripts Transcript by ASAP Sports
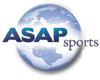

|